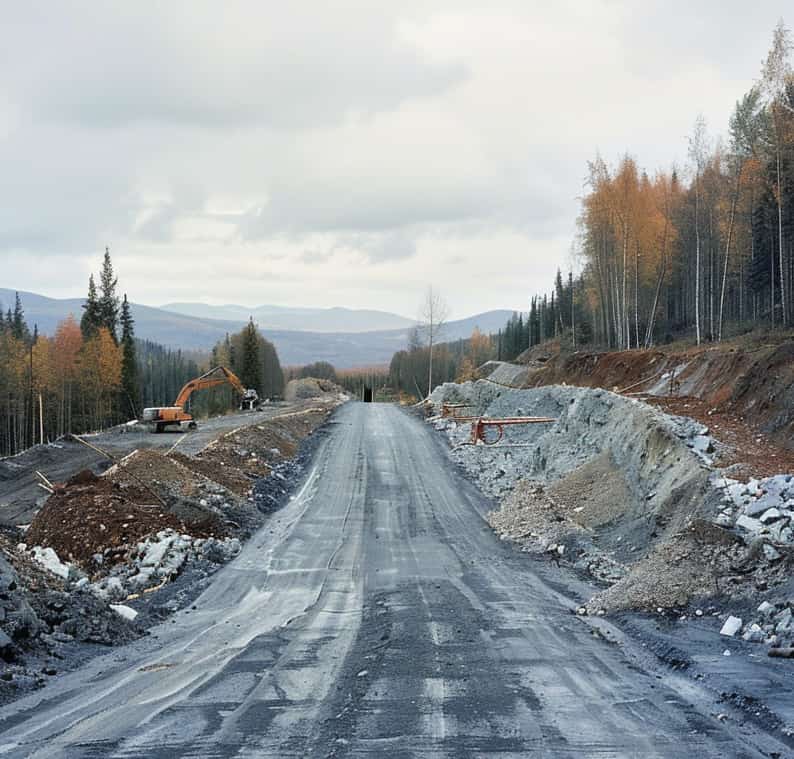
Today, let’s delve into the foundation of road construction: road base material. Not just any base, but one born from the resilience and reliability of granite.
At our quarry, the journey of road base material begins with the extraction of granite, an igneous rock known for its durability and strength. This isn’t just rock—it’s the future backbone of transportation. Our granite is systematically blasted, crushed, and sized to create a road base material that stands the test of time and traffic.
Road Base Materials Composition and Quality
Our road base material is predominantly composed of finely crushed granite mixed with smaller amounts of other rock aggregates. This mixture ensures a perfect balance between rigidity and flexibility—essential qualities to withstand various loads and weather conditions. We adhere to stringent quality control measures, guaranteeing that our road base material meets all the required specifications for grade, size, and safety.
Effective
Granite’s effectiveness as a road base material can be largely attributed to its geological characteristics and composition. Granite is a coarse-grained igneous rock formed from slowly cooled magma deep within the Earth’s crust. Its mineral composition—typically quartz, feldspar, and mica—provides a distinctive hardness and interlocking crystal structure, making it exceptionally sturdy and durable.
- Hardness and Weather Resistance: Granite ranks about 6 to 7 on the Mohs scale of mineral hardness, making it one of the harder natural stones. This hardness is crucial for road base applications as it provides a surface that is less susceptible to damage and abrasion caused by vehicular traffic. Furthermore, granite’s chemical stability means it is less likely to react with atmospheric pollutants or moisture, which enhances its resistance to weathering and erosion processes that can degrade other materials over time.
- Stress Distribution: The interlocking nature of granite’s crystalline grains plays a pivotal role in its ability to distribute loads. When a road base can effectively spread out the stress exerted by traffic, it prevents localized stress concentrations, which are often the precursors to structural failures such as rutting and deformation. This distribution is critical in maintaining the integrity and flatness of the road surface, providing a smoother and safer driving experience.
Road Base Materials Application and Versatility
Granite-based road base materials are not just beneficial for their durability but also for their versatility in various construction layers:
- Sub-Base Layer: In road construction, the sub-base layer acts as a stabilizer for the layers above. Granite road base material in the sub-base provides a strong and stable platform that enhances load-bearing capabilities and ensures proper drainage, which is vital for preventing water accumulation that could lead to structural weaknesses.
- Base Layer: Serving as the main load-bearing layer, the base layer of a road structure directly supports the surface layer (asphalt or concrete). Granite’s robust nature makes it an ideal choice for this critical layer. It ensures a firm foundation that can endure the direct pressure and friction from traffic, thus extending the lifespan of the road.
- Versatility in Application: The strength and adaptability of granite allow it to be used effectively in various settings—from heavily trafficked highways to less frequented rural roads. Each application benefits from granite’s inherent qualities, which ensure long-term performance and durability regardless of the traffic load or environmental conditions.
Sustainability and Cost-Effectiveness
Opting for granite road base material is not only a choice for quality but also a nod towards sustainability. Granite is abundantly available and requires minimal processing, reducing both environmental impact and costs associated with road construction.
Customization and Support
We understand that each road project carries unique challenges and requirements. That’s why we offer customized solutions in road base materials, tailored to meet specific project needs, whether it’s adjusting the blend of aggregates or matching precise gradation curves.
When it comes to building the arteries of transportation, the choice of road base material is paramount.
At Lynx Cat Mountain Quarry in Barstow, California, we are not just processing stone; we are crafting the underlayer of tomorrow’s roads—ensuring they are as solid, reliable, and enduring as the granite they’re made from. Choose granite for your next project, and lay the foundation for a road that stands firm, come what may.
Get a Quote
For a robust and reliable foundation in your next road construction project, choose granite road base materials from Lynx Cat Mountain Quarry. Contact us today to discover how our granite solutions can meet your project needs.